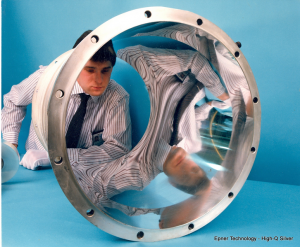
An early component from the “Star Wars” days. This so-called “pulsed compression cavity” was fabricated in aluminum, polished and then electroless nickel plated followed by .001” copper, which was highly polished again and finally a similar thickness of HiQ silver. This being a low-frequency device had a thicker silver than the normal .0005”
Epner technology was in the beginning of microwave itself. That was in 1938 when we were tasked with silver and gold plating the earliest “plumbing” as the wave guides and co-ax lines were then called, for systems that were being sent to England as an early warning system for the incoming German bombers during the Battle of Britain.
(See my blog “A Man with a Gun in My Daddy’s Factory”)
Both Hi-Q silver and a pure gold are used extensively for electronics and microwave hardware. The operating frequency of the hardware controls the skin depth and if the conductive coatings such as copper and silver are thick enough, then what is plated to prepare the substrate, nickel in the case of aluminum, beryllium or Albemet, has no effect on the microwave performance .
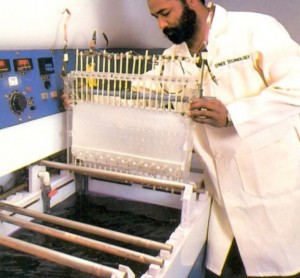
This unique set up for plating conductive materials (HiQ silver in this case) down into the bottom of some 20 individual filter cavities. In order to achieve uniform thickness distribution, four individual power supplies were applied to groups of five internal anodes. The anodes were pure silver rods.
QQ-365D
AMS-2410K, 2411H & 2412J
ASTM B 689-9